1) Primary lifting, fine screening and grit removal
Incoming industrial wastewater arrives directly in the lifting basin, so called as by there, eight pumps lift the sewage to the physical pre-treatment situated about 6 meters over, this, in order to exlploit the gravity flow down through the first treatment stages.
The fine screening removes all solids and hair bigger than 1,5mm or unable to pass through the 6 rotating cilindrical screens having this ports sizes.
The screened wastewater moves, then, to the 2 cyclonic grit removal systems, where residual inert solids and sands are settled and removed due to the exploiting of both gravity and centrifugal forces at the same time.
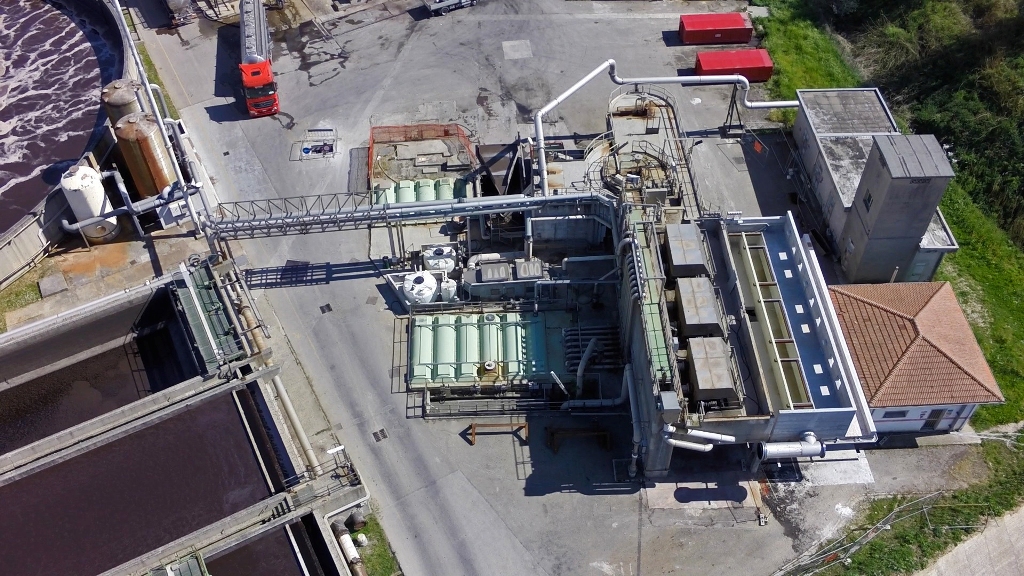
3) Biological oxidation - First stage
The first biological oxidation stage premises were built in 2001, specially for the conversion to the "Tutto Biologico" process. The conventional activated sludge (CAS) process exploits biological activity of spontaneous microorganisms (activated sludge) which, due to their adaptation and selectivity for the substrate, is able to degrade the pollutant substances dispersed among the sewage (substrate). In order to mantain the efficiency and the effectiveness of the biological process, it is mandatory to pay attention to biomass activity, strictly controlling main sewage parameters, in order to avoid the death of micro-organisms.
The main advantage of this kind of process is that smaller amount of sludge is produced than old physical-chemical process, because of the low dosage of chemicals.. On the other hand, large amount of air /oxigen needs to be blown through the sewage in order to maintain a high rate of oxigenation inside basins, this is the main requisite for aerobic biomass, which, as well as humans, requires oxygen to perform its metabolic pathways for the pollutants demolition.
Although the biological process requires less chemicals dosage, a strict control of the main parameters has to be performed. Characteristics of sewage are monitored more frequently than in a chemico-physical process, with the purpose to ensure the maximum efficiency of the activated sludge that, due to its nature, is susceptible to the toxicity of certain substances and to strong concentration flutuations, even in case of nutrients.
The first biological oxidation step of Consorzio Aquarno consists in two large rectangular basins of 15.000m3 each, that are identical both for structure and equipments. The aereation of the mixed liquor is ensured by two beds with 6.600 microbubbles diffusers each and feeded by 4 variable flow compressors.
Besides the several measuring systems present on field, the mixed liquor is regularly analyzed by the internal analytical laboratory in order to go over the parameters and work on the flows management. There are many possible actions to provide a precise control of the process, like the regulation of the activated sludge recycle from the sedimentation section, whose flow rate could influence both the treatment efficiency and the excess sludge production.