In 2001 the centralized WWTP constantly complyed with legal discharge limits and odours emissions were significantly below the tolerance threshold. However, these standards required large energy and chemicals consumptions (ferric salts and lime), consequently large production of physico-chemical sludge was obtained with high management costs. Furthermore, the construsction of new industrial zones in Santa Croce sull'Arno and Castelfranco di Sotto, would increased organic and hydraulic charges incoming the Aquarno premise. That further development needed another plan with a view to adequate the WWTP to the new hydraulic, managerial and environmental requirements. Thanks to the outcomes of a pilot plant simulating the substitution of the first physico-chemical stage with a biological one, the "Tutto Biologico" project began. Two biological oxidation basins of 15.000mc each were built up and they still represent the main difference between the old and the new plant. These two new tanks, together with other old structures, constituted the primary biological oxidation stage. The new plant arrangement was made up of two subsequential biological stages and a final physico-chemical treatment.
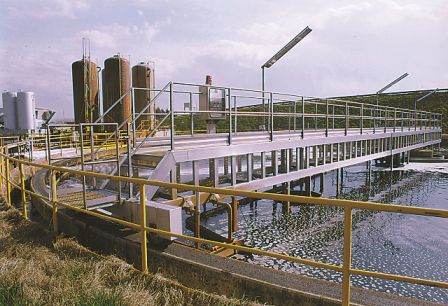

From the pre-oxidation step, wastewater are transferred to the new biological oxidation basins which works in parallel and are equipped, on their bottom, with a diffusers bed connected to a blower stations. Four compressors with variable flow-rate ensure the right LDO (Liquid Dissolved Oxigen) value within the tanks, where high rate of organic pollutant are removed due to the sewage long retention time. This condition also allows the demolition of a portion of organic sludge, reducing the overall production of this matrix. Alongside each oxidation basin there is a sedimentation tank where the biological sludge separation take place for the purpose of clarifying the wastewater and extracting the sludge which, then, can be recycled or evacuated. Sedimentation tanks were equipped with lamellar packs in order to save as much space as possible ensuring slow ascentional speed at the same time. Collected recycle sludge is partially transferred to the oxidation basins and the other rate is pumped to the pre-oxidation basins in order to ensure high and constant concentration of suspended sludge within the primary biological oxidation section. Clarified wastewater flow to an intermediate tank from where it is pumpued to denitrification and then the secondary biological oxidation stage. Within this last biological step a further degradation of oranic pollutants occur and ammonium nitrogen is oxidised and eliminated because of the specific biomass and conditions created inside the basins. As substitution of old superficial aeration system, six microbubbles diffusers beds were installed and fed by four new blowers , the new ssytem brought sevral advantages: firstly the environmental ones as the reduction of biological aerosol, in the second place a better oxygen distribution and biomass efficiency were possible; thirdly maitenance operations were easier and less frequents. Biological sedimentation basins were the same and no modification occured to this stage, ans well as to the tertiary physico-chemical treatment and the final coagulation stage. The new "Tutto Biologico" process not only will improve the depuration yelds, but also makes it possible to use the "Fenton" tertiary physico-chemical treatment only in case of emergency, avoiding, this way, the consumption of large amount of chemicals and the corresponding production of sludge. The main purpose of "Tutto Biologico" process is the conservation of the high treatment efficiency gained through plant evolution steps, reducing, at the same time, chemicals utilisation and excess sludge production. The use of a biological stage as first treatment step for the incoming wastewater, enable to save chemicals and degrade the majority of soluble COD reducing also the suspended solids content and producing an easy settleable biological sludge.